Reducing scope emissions at refineries: A closer look into utilizing energy efficiency profitably
In 2001, Green House Gas (GHG) Protocol coined the term scope 1, 2 and 3 emissions to guide industries, cities and governments in formulating their strategies to reduce carbon footprint.
What are scope 1, 2 and 3 emissions and how do they relate to a refinery operation?
- Scope 1 emissions: The direct GHG emissions by company-owned resources. For example, emissions caused by burning fuel gas into a fired heater, flaring and more.
- Scope 2 emissions: The indirect GHG emissions associated with purchasing utilities. For example, purchased electricity, rental chillers, purchased cooling water and more.
- Scope 3 emissions: The indirect GHG emissions (not included in scope 2 emissions) that occur in a company's upstream and downstream value chain. For example, emissions caused by refined products, business travel by employees and more.
Most refineries in the United States are now setting goals and formulating strategies to reduce their carbon footprint. While there are various routes to achieve this goal, one of the key solutions is energy efficiency. Download the checklist for fractionation columns to learn how to maximize heat exchanger efficiency.
The International Energy Agency (IEA) estimates that:
"Energy efficiency represents more than 40% of the emissions abatement needed by 2040. Energy efficiency is the "first fuel": Reigning in the scale of this unprecedented challenge, supporting net zero energy goals at lower costs, and delivering a wide array of benefits for society."
The good news is that the technologies to attain sustainability goals through energy efficiency are available here and now, and it is the cheapest available tool at hand that a refinery can start implementing right away. Energy efficiency, in most cases, also helps a refinery reduce its carbon footprint and make more profit.
Determining the right energy efficiency opportunities is key
An essential first step when utilizing energy efficiency as a tool towards reducing carbon footprint and increasing profit is identifying the right energy efficiency opportunities that make the best economic sense. Get started on identifying these opportunities with this essential checklist for fractionation columns.
At this stage, a refinery can take two approaches in their quest for energy efficiency:
1. Strategic approach
In this type of approach, a refinery consciously develops projects focusing on energy efficiency and energy efficiency becomes one of the key performance indicators of a process unit or a project investment (grass root or revamps). This approach is geared towards making a major impact on EII (Energy Intensity Index). Examples include crude preheat train redesign to a tighter pinch reducing furnace duty or waste heat pickup from air coolers (condensers or product coolers) to boiler feed water.
2. Opportunistic approach
In this type of approach, a refinery evaluates if they can club energy efficiency with every expenditure opportunity. When a refinery plans to spend money to run the unit safely and reliably anyway, why not spend the money strategically on energy efficiency and reduced emissions and utilities? Examples include bundle replacement, metallurgy upgrade, heat exchanger end of life, small improvement projects, more heat recovery on a feed/bottoms interchanger or recovery waste heat from overhead condenser with compact plate heat exchanger instead of like-to-like bundle replacement.
How to reduce scope 1, 2 and 3 emissions in your refinery using energy efficiency
Whether you’re an Energy Coordinator or Process Engineer looking to identify similar opportunities in your refinery, this series can provide you with concepts and case stories to guide you in the right direction. Learn more about how to maximize heat exchanger efficiency.
Discover how Alfa Laval can help to reduce your carbon footprint - while increasing your profits - by visiting:
- Enabling sustainability goals of renewable fuels projects
- Energy efficiency opportunities around different heat exchanger positions in a fractionator - Part 1
- Energy efficiency opportunities around different heat exchanger positions in a fractionator - Part 2 (coming soon!)
Ready to reduce your carbon emissions? Our team of experts is standing by to help you identify cost-effective solutions in your refinery. Contact us today and start making a difference!
Webinar on demand
Looking to reduce your refinery’s carbon intensity? Do you also need to increase profitability at the same time? Watch our webinar to learn how to make this happen by using welded plate heat exchanger technology.
Read other relevant refinery blog posts
How to cut your refinery cooling water consumption by 30-50%
Reduce carbon intensity while improving bottom line in the refining sector
Overcome the challenges of cooling desalter water effluent
Debottleneck naphtha hydrotreaters with highest project ROI
Refinery alternatives to box coolers
Reducing energy consumption in industrial refrigerant systems
Benefits of Compabloc technology versus shell & tube
Using Packinox heat exchanger for catalytic reforming
Efficient wastewater cooling and reuse
Enabling sustainability goals of renewable fuels projects
Reducing scope emissions at refineries: A closer look into utilizing energy efficiency profitably
Energy efficiency opportunities around different heat exchanger positions in a fractionator – Part 1
Sumit Chintawar
Sumit Chintawar is a Cleantech Business Development Manager for the Energy Division at Alfa Laval, with over 10 years of refinery industry experience in the Middle East, India and the US. He holds a degree in Mechanical Engineering from Nagpur University and a Master’s in Business Administration from ICFAI Business School, India. Sumit is helping US refineries implement welded technology for process reliability and sustainability improvements, reducing utilities and project capex.
Connect with Sumit to learn more about his expertise in the refinery industry.
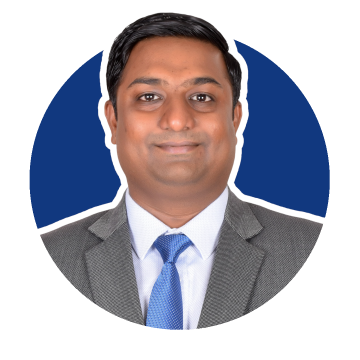