Reduce carbon intensity while improving bottom line in the refining sector
Interest in renewable fuels, including renewable diesel, continues to grow because of regulations and industry pressure to reduce the carbon content of fuels. While there are incentives in the market that reward investors in creating energy efficient plants, traditional process design philosophies and technology applications prevent them from reaching this goal.
What is the strategy to reduce carbon intensity?
The strategy to reduce carbon intensity (CI) must focus on reducing the amount of natural gas, electricity and chemicals required in the production of renewable fuels. In producing renewable fuels, there are simple ways to increase energy efficiency due to the highly exothermic nature of the process. A process designer can use this exothermic energy to create high pressure steam to supply process heating needs to minimize the need for natural gas. However, if the goal of the project is to create a process with the lowest practical CI, this alone will not be enough.
Alfa Laval has found there is a significant amount of low-grade energy that is typically wasted to utilities that can reduce the CI. However, there is often little interest when a traditional, cost-benefit energy analysis is utilized. We have also seen there are multiple process licensors involved who may optimize their section of the facility, but often times, nobody is tasked with the overall responsibility of integrating the entire facility. This makes each part of the plant optimized, but the overall facility is sub-optimized.
Below is a strategy with three simple steps that can ultimately reduce the amount of natural gas/electricity needed to reduce the carbon intensity of the plant.
Step 1: Maximize the process of heat integration
The project owner needs to drive the goal of a low CI across the design of the entire plant. The proposed process designs will include heat integration based on traditional heat exchanger design philosophy. In the initial project meetings, the project owner should communicate priorities with the process licensors for the feed pre-treatment, hydrogen and renewable diesel processes to minimize cooling utilities by maximizing the heat integration.
Welded plate heat exchanger technology can recover energy with incremental costs that were previously not available. The project owner should look for every opportunity to reduce the amount of energy needed for natural gas or electricity in furnaces, reformers, compressors, pumps, fractionation towers, cooling towers, air coolers and cooling water coolers.
Step 2: Create energy systems
The project owner should take the remaining energy that now requires removal from the process and find methods to put it into energy systems. By utilizing welded plate heat exchangers to cost effectively allow close temperature approaches, energy systems can be created with the maximum amount of energy extracted/inputted into the process. Options to consider include:
- High pressure steam: This energy is highly valuable and should be used where maximum impact in reducing carbon intensity is optimal. Most customers look at options of power generation with this energy.
- Low pressure steam: This energy can be used within the process, as well as the outside battery limits (OSBL), to provide most of the energy needed for production needs. Good examples of this include heating in the pretreatment process, sour water stripper and amine systems.
- Hot water loops: The feed streams for renewable diesel have difficulty flowing at ambient temperatures requiring energy to heat tanks, process lines and the loading/unloading systems. In some locations, it may also be valuable to create district heating systems to use this energy. Hot water loops are an accepted industry standard to move low grade heat to places where it is needed while minimizing utility cooling.
We have seen a renewed interest in mechanical systems such as organic Rankine cycle or adsorption chillers to use this waste heat. Traditionally, it has been hard to justify these processes, but with new economic incentives tied to carbon credits, these options are now becoming cost effective.
Step 3: Reduce utility cooling
If this energy system is designed properly, there will be no more practical energy to recover, giving process outlet temperatures a range of 150-160oF.
Most process design engineers would typically reduce the process temperature to 130oF with an air cooler, requiring capital costs and electricity. Final cooling would then be done with a shell and tube heat exchanger with cooling water as the side fluid medium. This process expends a large amount of electricity and leads to high operational costs in chemicals and heat exchanger maintenance.
Alfa Laval studies have shown that after completing the first two steps, the final cooling in step three can be completed with a closed loop system that combines welded plate technology and the Niagara Wet Surface Air Cooler. This provides a double benefit to the project:
- Elimination of CAPEX that would typically be spent on air coolers and water pretreatment systems.
- Reduction of OPEX that is traditionally spent on the treatment of fresh water. This reduces the overall electricity usage by 60% and reduces the cooling water chemical addition by 60%.
Ultimately, the use of welded plate heat exchanger technology, in conjunction with an aggressive carbon intensity reduction strategy, will allow customers to make incremental investments and realize returns that will reduce carbon intensity and build a sustainable future while improving their bottom line.
Read other relevant refinery blog posts
How to cut your refinery cooling water consumption by 30-50%
Reduce carbon intensity while improving bottom line in the refining sector
Overcome the challenges of cooling desalter water effluent
Debottleneck naphtha hydrotreaters with highest project ROI
Refinery alternatives to box coolers
Reducing energy consumption in industrial refrigerant systems
Benefits of Compabloc technology versus shell & tube
Using Packinox heat exchanger for catalytic reforming
Efficient wastewater cooling and reuse
Enabling sustainability goals of renewable fuels projects
Reducing scope emissions at refineries: A closer look into utilizing energy efficiency profitably
Energy efficiency opportunities around different heat exchanger positions in a fractionator – Part 1
About The Author
Mike Buettner
Mike Buettner is a Refinery Welded Plate Technologist and works with US refineries to implement heat exchanger technology. Mike has worked in the refinery industry for over 25 years, both in the United States and Asia, in various roles within EPC’s, refineries, and technology solution providers. Mike has a degree in Chemical Engineering from Michigan Technological University and a Master’s in Business Administration from the University of Minnesota.
View Carbon Intensity Webinar
Our refinery experts offer case study insights to reduce carbon intensity and achieve sustainability goals with Alfa Laval welded heat exchangers.
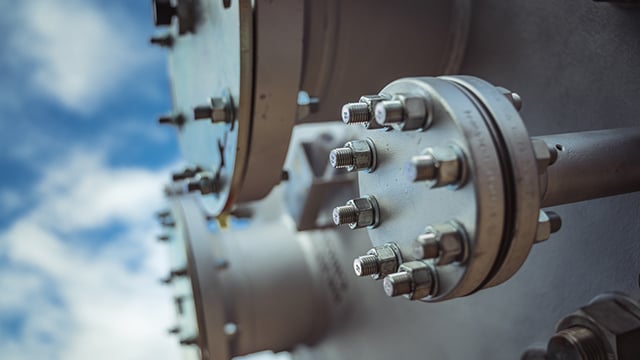
Renewable fuels production
In the quest to minimize the environmental impact of refinery products such as diesel, jet fuel and naphtha, more refineries are transforming their plants to operate with renewable feedstocks. To produce fuels with equivalent or even higher qualities than today, hydrotreated vegetable oil (HVO) processing is quickly becoming the preferred solution for such production