Enabling sustainability goals of renewable fuels projects
Driving by a refinery or petrochemical facility, it is hard not to notice the mirage floating over the facility, which is formed by waste heat being exhausted by the furnaces and air coolers. On the other side of the process unit, white plumes of evaporated water reach for the sky, which is waste energy being transferred into the air. These are visible signs of energy that is either generated or inputted into the process and is now being sent into the environment. As sustainability is becoming more of a focal point for our industry, seeing this visible sign of waste energy makes you wonder if there is a better way to design our processes to minimize the losses. Questions that may come to mind include:
- Where in the process is this energy coming from?
- What could have been done differently to reduce this energy loss?
- Why wasn’t it recycled back into the process instead of being expelled to the environment?
To answer these questions, we need to go back to the inception of the project.
Energy balance
During the process design, one of the tools that our industry utilizes to maximize energy efficiency is called a Pinch Analysis. Hot and cold streams are matched with the goal of maximizing heat recovery and, therefore, minimizing the waste energy. The project assumes costs associated with energy – traditionally steam, electricity and fuel gas, but, more recently, we have started to see the price of carbon be included as well. As this analysis progresses, several business cases are formed that match a CAPEX required to achieve a certain level of benefit. A curve that looks like the one below (Figure 1) will be created:
Figure 1: Cost/Benefit Analysis
The optimal “pinch” is achieved when the analysis shows that CAPEX spent is no longer justified for the benefit achieved. The energy that cannot be matched to process streams in the process is typically handled in two ways:
- Generates steam that can be used in other parts of the process and/or facility.
- Removed from the process with air and water coolers and added back into the environment heat sync.
Heat exchanger technology
Heat exchangers are the primary equipment that is used to match these hot and cold streams. The optimal pinch is based on a set of performance expectations that our industry has grown to accept for the heat exchangers in the process. The main heat exchanger that is used by our industry, the shell-and-tube exchanger, was developed at the start of the industrial revolution over 200 years ago. While the expectations on the efficiency of our processes have changed drastically since then, and will only continue to grow in the future, our industry’s performance expectations of heat exchangers have not.
Alfa Laval has worked with the refinery industry for more than 30 years; raising performance expectations for their heat exchangers by using welded plate heat exchangers. One of these solutions, the Compabloc, is a heat exchanger that is three to five times more efficient than the traditional shell-and-tube heat exchanger. This increased performance reframes the Pinch Analysis and allows the process designers to achieve energy efficiency levels that were not cost effective with traditional heat exchanger technology. The result is integration of more energy back into the process, minimized utilities and, in the end, minimized amounts of process waste heat. Specific examples of these solutions can be seen in our previous blogs, as well as reaching out to one of our refinery technologists to discuss further.
Managing process waste heat
Assuming we have designed a process with the smallest pinch possible with the use of our welded plate heat exchangers, the next discussion we have with our clients is what to do with the remaining process waste heat. The typical decision is that a good result has been achieved, and the implementation of the traditional cooling philosophy of using air and water coolers is used. (Figure 2) While this is easy to implement, we feel that there is more that can be done with this waste energy.
Figure 2: Typical Waste Heat Cooling System
Energy Dome
We have worked on projects with customers where they had goals to reduce carbon intensity, and one topic that we bring up in conversation is how to utilize low grade process waste heat. There are two common challenges that come up during this discussion:
- Transportation: The location of this waste energy is throughout the facility, but the heat syncs are typically not in the same location.
- Heat Syncs: There is a large amount of energy available in this process waste heat, however, the temperatures tend to be low, making it difficult to find a match for this energy.
These two challenges will stop most projects from pursuing this route as traditional technology will not make this feasible; but changing the approach by using welded plate heat exchangers makes this type of energy extraction possible. This has led Alfa Laval to a concept that we have developed called our “Energy Dome.” (Figure 3)
Figure 3: Energy Dome Concept
By combining two of Alfa Laval’s industry leading welded heat exchanger technologies, the Compabloc and the Niagara Wet Surface Air Cooler (WSAC), we solve the transportation issue, allowing our customer to control the use of their process waste energy.
- The efficiency of the Compabloc allows for the highest possible hot water temperatures, targeting 210 °F, while cooling the process stream to its final outlet temperature, in a single unit.
- The WSAC allows for the hot water loop to be reduced to the same temperature as would be produced by a cooling tower, eliminating the need for a separate cooling system.
- Water make-up for the WSAC can be from process water streams in the plant eliminating the need for fresh water make-up.
- We find the overall energy needed to drive electrical motors decreases, reducing carbon intensity.
- The number of units that need to be installed is reduced by more than 50%, resulting in simplified construction and a lower TIC. If the system is modular, the savings can be dramatic.
The next challenge that needs to be solved is finding heat syncs, which will need to be left to the imagination of the process designer and the needs of the project. Common heat syncs that Alfa Laval has supported customers with include:
- Boiler Feed Water Preheating
- Air Preheating for Furnaces
- Renewable Diesel Pretreatment Utilities
- Zero Liquid Discharge (ZLD) Systems
- Desalination Systems
- Tank Heating
- Organic Rankine Cycle (ORC) Power Systems
I have personally worked on several ORC projects and none of them have moved forward. In today’s environment of carbon credits and social capital, I believe these could become an interesting part of a process design. In exothermic processes like renewable diesel, there is enough low-grade process energy to generate the necessary electricity to power the entire Energy Dome system.
About the Author
Mike Buettner
Mike Buettner is a Refinery Welded Plate Technologist and works with US refineries to implement heat exchanger technology. Mike has worked in the refinery industry for over 25 years, both in the United States and Asia, in various roles within EPC’s, refineries, and technology solution providers. Mike has a degree in Chemical Engineering from Michigan Technological University and a Master’s in Business Administration from the University of Minnesota.
Salt water and extreme environment applications
Read our case story about one customer we’ve worked with to provide sustainable plant cooling in extreme conditions.
Improving the sustainability and profitability of renewable diesel
Renewable fuels production
In the quest to minimize the environmental impact of refinery products such as diesel, jet fuel and naphtha, more refineries are transforming their plants to operate with renewable feedstocks. To produce fuels with equivalent or even higher qualities than today, hydrotreated vegetable oil (HVO) processing is quickly becoming the preferred solution for such production
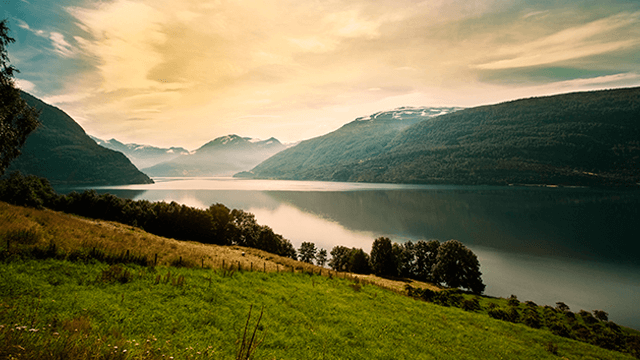
Read other relevant refinery blog posts
How to cut your refinery cooling water consumption by 30-50%
Reduce carbon intensity while improving bottom line in the refining sector
Overcome the challenges of cooling desalter water effluent
Debottleneck naphtha hydrotreaters with highest project ROI
Refinery alternatives to box coolers
Reducing energy consumption in industrial refrigerant systems
Benefits of Compabloc technology versus shell & tube
Using Packinox heat exchanger for catalytic reforming
Efficient wastewater cooling and reuse
Enabling sustainability goals of renewable fuels projects
Reducing scope emissions at refineries: A closer look into utilizing energy efficiency profitably
Energy efficiency opportunities around different heat exchanger positions in a fractionator – Part 1