The Alfa Laval Packinox heat exchanger for catalytic reforming
The Alfa Laval Packinox heat exchanger for Catalytic Reforming
Catalytic reforming is a refinery process where low octane naphtha feedstock is reformed (meaning, molecules are rearranged) at high temperatures in reactors containing different catalysts to form a high-octane stream known as reformate. It is an energy intensive processes in an oil refinery and produces approximately 30 percent of the gasoline pool plus a significant amount of the hydrogen used in other refinery processes such as hydrotreaters and hydrocrackers. This blog illustrates how welded plate heat exchangers compare with traditional technologies in the catalytic reforming process.
The catalytic reforming process (see figure 1, generic flow diagram) benefits from the use of a feed / effluent exchanger position where the naphtha and recycle gas recover some of the heat from the effluent which reduces the fired heater duty. This position has traditionally been served by complex banks of horizontal shell and tube exchangers with parallel and series arrangement. In the 1970’s, there was an improvement in energy recovery when process licensors and refineries switched to using Vertical Combined Feed Effluent (VCFE) exchangers also known as Texas Towers.
Figure 1. Simplified Catalytic reforming process
Oil refineries have been using welded plate heat exchangers in their catalytic reformers since the late 80’s with the intent of improving refinery profitability beyond what any other technology could offer. Achieving this profitability has been validated by major licensors because of the welded plate heat exchanger’s high efficiency capabilities in heat transfer. This has resulted in considerable energy savings, a decrease in emissions and greater yields of high-value streams.
The Packinox® is Alfa Laval’s welded-type plate heat exchanger offering for the catalytic reforming process. The term “welded” means there are no gaskets between the corrugated plates (see figure 2) The plates are welded to each other on the extremes, forming channels for the feed side and the cold side. The multiple channels form a bundle which is inserted inside a pressure vessel—also known as shell. The gap, or distance between plates, can vary between 3 to 8 mm. This small gap, together with the corrugations, provides very high turbulence which enhances the heat transfer coefficient; however, it requires the fluids to be very clean to avoid plugging of the channels and to minimize fouling.
Figure 2, Packinox heat exchanger cutaway
Retrofitting a Packinox exchanger into an existing catalytic reformer has proven to be a simple way to revamp the operation of the catalytic reformer for either increasing liquid yield or octane number without other major changes in other equipment such as recycle gas compressor or fired heaters
A Packinox heat exchanger, by design, has a lower pressure drop compared to shell-and-tubes so the catalytic reformer can operate at lower pressure thereby increasing the yield.
Another factor that influences the yield is the recycle gas to liquid feed ratio (also known has H2/HC ratio). Refiners have variable operating conditions and, at times, this ratio needs to be lower than normal, but it is critical that the recycle gas flow rate is sufficient to lift all the liquid feed droplets through the heat exchanger. The corrugated plate construction of the Packinox, plus the use of a proprietary Liquid Lift Controller, reassure the operator of a successful operation.
Example – Revamp of a 30,000 BPD Continuous Catalytic Reformer Unit
|
Shell & Tube HEX |
|
Packinox HEX |
Number of shells |
2 |
1 |
|
Duty |
143 MMBtu/h |
|
157 MM Btu/h |
Additional heat recovery |
|
|
14 MM Btu/h |
CAPEX |
|
|
|
Equipment cost |
$ 2,700,000.00 |
$ 2,530,000.00 |
|
Installation cost |
Replace in kind |
|
$ 1,100,000.00 |
Total Installed cost |
$ 2,700,000.00 |
|
$ 3,630,000.00 |
OPEX |
|
|
|
Fuel savings per year* |
|
|
$ 952,966 |
Payback time, months compared to replacement in kind |
|
11 Months |
|
Total savings after five years operation |
|
|
$ 2,087,793 |
Key takeaways:
- Packinox exchangers have been used by many refiners worldwide since the late 80’s.
- Due to it’s corrugated plate construction, the Packinox exchanger is able to achieve better performance in terms of heat recovery when compared to traditional Shell and Tube exchangers in vertical configuration.
- Retrofitting a Packinox exchanger in an existing catalytic reformer is the most simple way to revamp this unit at a low capital expense.
On the next posts I will discuss important details about the operation and maintenance of the Packinox exchanger with the purpose of assuring its operational reliability.
For more information and evaluation of a potential fit, please contact your regional Alfa Laval Packinox Sales Manager.
About the author
Packinox - How it works
Why Packinox?
A Packinox enables higher yield and recovers more heat than a shell-and-tube solution, resulting in better ROI and a lower environmental impact.
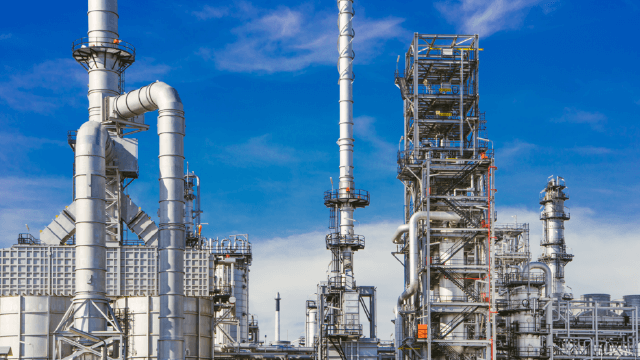
Read other relevant refinery blog posts
How to cut your refinery cooling water consumption by 30-50%
Reduce carbon intensity while improving bottom line in the refining sector
Overcome the challenges of cooling desalter water effluent
Debottleneck naphtha hydrotreaters with highest project ROI
Refinery alternatives to box coolers
Reducing energy consumption in industrial refrigerant systems
Benefits of Compabloc technology versus shell & tube
Using Packinox heat exchanger for catalytic reforming
Efficient wastewater cooling and reuse
Enabling sustainability goals of renewable fuels projects
Reducing scope emissions at refineries: A closer look into utilizing energy efficiency profitably
Energy efficiency opportunities around different heat exchanger positions in a fractionator – Part 1