Reducing energy consumption in industrial refrigerant systems
Refrigeration has been one of engineering’s great gifts to humanity since the early nineteenth century. The process is well-understood and has found many practical applications. It is used in food preservation, climate control for comfort and as a coolant for various chemical processes. In fact, some of the largest refrigeration systems in the world are used in the manufacturing of natural gas, fuels like alkylate, and basic chemicals like ethylene and propylene. This blog will address the optimization of these large refrigeration processes through application of various Alfa Laval heat exchanger technologies.
The refrigeration cycle can be simply explained as a combination of four process steps:
- Gas compression
- High pressure condensation
- Expansion
- Low pressure Evaporation (chilling)
The theoretical representation of these steps is popularly known as the Carnot Heat Cycle (Figure 1.) where heat exchangers are responsible for rejecting the heat of condensation to the atmosphere as well as absorbing heat from the fluid or process being chilled.
Figure 1. Heat flow diagram for Carnot cycle refrigeration
Alfa Laval is the world leader in optimizing refrigeration systems and has offered the standard heat exchanger solution for commercial and residential refrigeration systems for decades. However, industrial refrigeration users have been slower to adopt the more efficient Alfa Laval technologies ubiquitous to other refrigeration systems. Why? Maybe Alfa Laval technologies that had been well-adapted for light industry or commercial use in the past, have not been well-suited for industrial use. This has since been addressed by the introduction of welded plate technologies such as the Compabloc and industrial evaporative coolers like the Niagara Wet Surface Air Cooler (WSAC), both finding wide application in the refining and chemical industries. Another limit is the conservative nature of the industry—where outdated rules of thumb are applied, resulting in reliable, but far from optimum, process designs. Fortunately, Alfa Laval can offer solutions to help optimize plant refrigeration systems using proven and reliable technologies.
Illustrating the challenges:
In Figure 1, P1 and P2 are set by the required chilling temperature and the ambient air conditions, minus some approach temperature of the chosen heat exchanger technology. This also sets the compression load to raise pressure from P1 to P2. Furthermore, if Shell & Tube (S&T) heat exchangers are used as the condenser, a limitation exists where the cooling medium outlet temperature cannot cross the refrigerant subcooling temperature (Figure 2). The results? Higher P2 is required to achieve the minimum temperature difference and exorbitant amounts of cooling water are required to avoid heating the coolant above the subcooled refrigerant temperature.
Figure 2. S&T Temperature profile. Note the temperature approach limits and coolant outlet temperature limit
Optimize condenser performance:
It is possible to reduce the condensing temperatures by employing Alfa Laval heat exchanger technologies as the refrigeration condenser.1 For every 1° F reduction in condensing temperature, compressor input power is reduced by 1.5%-2%; so, the potential exists for a welded plate heat exchanger, as a condenser, can lower power consumption in the compressor by 15-20%. In addition, it is possible to condense and sub-cool while heating the cooling medium to the maximum safe temperature, lowering coolant flow by 50-60% or more (Figure 3). This has CAPEX and OPEX impacts in reducing line sizes and lowering circulating cooling water pump power.
Figure 3. 15-20% compressor power savings possible by employing Compabloc technology
If circulating cooling water is not used as the coolant for the condenser, Alfa Laval recommends the Niagara Wet Surface Air Cooler (WSAC) as an evaporative cooler for industrial processes (Figure 4). The concept is not new as evaporative coolers are used frequently in the commercial refrigeration industry as condensers. The primary advantage of the WSAC is it uses the ambient Wet Bulb temperature to directly condense the refrigerant. It is possible to achieve a 10F (6C) approach to the wet bulb temperature by using a WSAC as the condenser—lower than even the Compabloc using indirect cooling water. It really is the ideal solution for maximizing efficiency of industrial refrigeration systems.
Figure 4. Niagara Wet Surface Air Cooler as refrigeration condenser
Building an industrial evaporative cooler to withstand the rigors of a process plant environment requires a more robust solution than what is widely employed in the commercial HVAC industry today. Alfa Laval Niagara has decades of experience designing, constructing and operating WSAC for refinery and petrochemical customers; their design is tailored specifically to address the challenges of industrial plant environments.
In conclusion, Alfa Laval has taken their decades of knowhow in refrigeration applications and successfully applied them in refineries and chemical plants around the world. Contact us to see for yourself how Alfa Laval can optimize your industrial refrigeration system with our technologies.
References:
1. Nigro, Ralph (2020) Energy Efficiency Opportunities in Industrial Refrigeration. University of Delaware Industrial Assessment Center with the US EPA
Read other relevant refinery blog posts
Debottleneck naphtha hydrotreaters with highest project ROI
Overcome the challenges of cooling desalter water effluent
How to cut your refinery cooling water consumption by 30-50%
Refinery alternatives to box coolers
Reduce carbon intensity while improving bottom line in the refining sector
Reducing energy consumption in industrial refrigerant systems
Benefits of Compabloc technology versus shell & tube
About the author
Chris Wajciechowski
Chris Wajciechowski is Business Development Manager for Alfa Laval, applying high-efficiency and problem-solving heat exchangers in the Refining industry for over 20 years. His focus is on improving process performance and increasing reliability, thereby improving the profitability of refineries worldwide. Chris holds a Bachelor of Science in Chemical Engineering from Virginia Tech and is a licensed Professional Engineer in the USA.
Why Compabloc?
There are more than 500 Compablocs installed around the world working as cooling water exchangers in crude oil refinery, saving millions of gallons of cooling water every year.
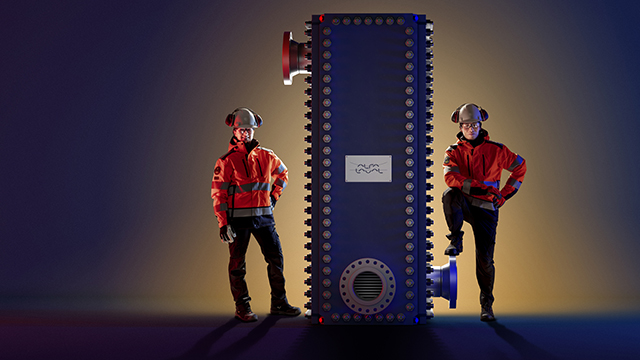
Niagara Wet Surface Air Cooler
Alfa Laval Niagara Wet Surface Air Coolers (WSAC®) are custom built, closed-loop cooling and condensing systems that combine high performance, low operating costs, compact size and reliable operation. Renowned for their robust design and high efficiency, Alfa Laval Niagara WSACs are used in a large number of demanding industries. Their low water consumption and high cooling capacity have made them a popular choice in applications where low temperatures are required for process improvements.
Compabloc
This animation demonstrates how the welded plate-and-block heat exchanger, Alfa Laval Compabloc, functions when operating as a 2-pass condenser for low pressure vapours. Discover how you can improve sustainability with Alfa Laval Compabloc - an unrivalled champion that stands out among other heat exchangers, including other welded bloc-type designs. The difference comes from unique innovations that Alfa Laval has developed based on our decades of experience in thermal transfer. These features enable more reliable and efficient performance, helping you to save energy and improve your sustainability.