Sulfuric Acid Alkylation
In this refinery application series on Sulfuric Acid Alkylation; explore how Alfa Laval's welded heat exchanger technologies have been applied to debottleneck, increase capacity, reduce CAPEX, increase energy efficiency & reduce utilities.
Application Leaflet
Whether your refinery is adding a new alkylation unit or revamping an existing one, you need an optimal process design to minimize project cost and maximize the efficiency of your processes.
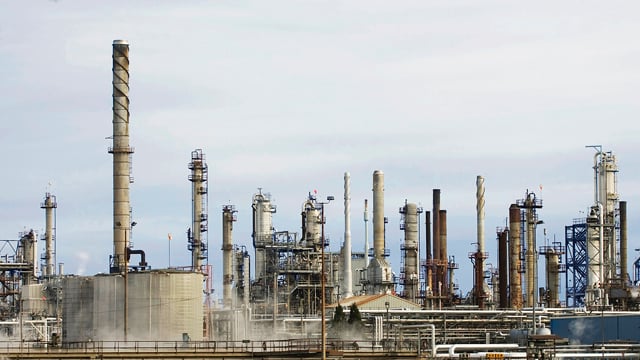
Blog post
Optimizing large industrial refrigeration processes is possible through the application of various Alfa Laval Heat Exchanger technologies. Read the blog: Reducing energy consumption in industrial refrigerant systems
Webinars
Boosting Sulfuric Acid Alkylation Performance
Alkylation processes are an important tool for refineries to create octane that is required to meet gasoline specifications. In recent years with Tier III regulations implementation, and the resulting destruction of octane in hydrotreating processes, the need for more octane has never been stronger.
How to optimize sulfuric acid alky reactor section by optimizing feed to effluent heat exchanger
How to optimize sulfuric acid alky refrigeration section by optimizing refrigerant condenser
How to optimize sulfuric acid alky Deisobutanizer section by optimizing DIB overhead condenser
Read other relevant refinery blog posts
Debottleneck naphtha hydrotreaters with highest project ROI
Overcome the challenges of cooling desalter water effluent
How to cut your refinery cooling water consumption by 30-50%
Refinery alternatives to box coolers
Reduce carbon intensity while improving bottom line in the refining sector
Reducing energy consumption in industrial refrigerant systems
Benefits of Compabloc technology versus shell & tube