Decanters
Alfa Laval decanter centrifuges help you with solid-liquid separation within one single continuous process. Stand out from the competition with high performance separation that results in extracted/clarified products of excellent quality and higher commercial value. Make a difference as you recover valuable raw materials, reduce energy consumption and lower footprint and waste management costs with our industrial decanter centrifuge machines and services.
Make a difference to your business and the environment:
- High-performance separation, resulting in high-value products and low waste management costs
- Low energy consumption and carbon footprints
- Low maintenance costs thanks to continuous operation, high-grade machine materials, smart design and well-thought preventive services
- Low capital cost/capacity ratio
Solid-liquid separation is a common manufacturing process and Alfa Laval has more than 60 years of experience in decanter centrifuge uses to meet this requirement in various industries. Together with our industry know-how and specialist process experience from all over the world, Alfa Laval can match your exact needs for each particular application and installation.
How does a decanter centrifuge work?
Solid-liquid separation - Innovation using centrifugal force
Separating solids from liquids plays a key role in countless industrial processes. Traditionally, many businesses use a clarifier or settling tank, in which particles, sediment and solids gradually fall to the bottom due to the force of gravity. However, such clarification is an extremely slow process with not so controllable results.
To accelerating the process, decanter centrifuge operation makes use of centrifugal force – the effect can be up to 4000 times greater compared to using gravitational forces. Solid-liquid separation can also be easily controlled by adjusting the speed of rotation.
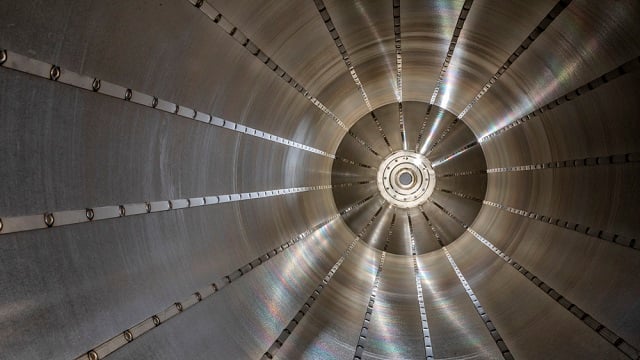
What happens during solid-liquid separation using our decanter centrifuge? Subject to centrifugal forces, the denser solid particles are pressed outwards against a rotating bowl wall, while the less dense liquid phase forms a concentric inner layer in a decanter centrifuge. Different dam plates are used to vary the depth of the liquid – the so-called pond – as required. The sediment formed by the solid particles is continuously removed by the screw conveyor, which rotates at a different speed than the bowl. As a result, the solids are gradually “ploughed” out of the pond and up the conical “beach”.
The centrifugal force compacts the solids and expels the surplus liquid. The dried solids then discharge from the bowl. The clarified liquid phase or phases overflow the dam plates situated at the opposite end of the bowl. Baffles within the centrifuge casing direct the separated phases into the correct flow path and prevent any risk of cross-contamination.
The speed of the screw conveyor may be automatically adjusted by use of the variable frequency drive (VFD) in order to adjust to variation in the solids load.
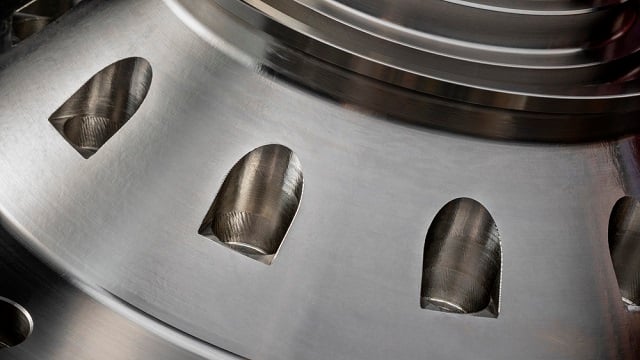
Benefits
What are the benefits of decanter centrifuges compared to other types of separation equipment?
Faster separation in single continuous process
Our horizontal centrifuges separate solids from one or two liquid phases in one single continuous process in a continuous, high-speed process. This enhances productivity and thus, profitability.
Wide-ranging feed variations and controllable performance
Alfa Laval centrifugal decanters are designed to handle a wide range of solid particles with diameters from 5 mm to a few microns.
Our industrial decanter units can also handle slurries with a solid content from as low as 0.1% w/w to more than 65% w/w.
Controllable centrifugal forces and other specific configuration details mean process optimization according to your specific requirements and goals, such as end-product of high market fit at the lowest possible costs.
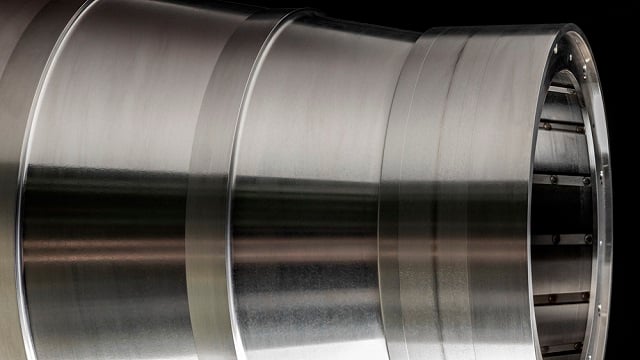
Decanter Centrifuge Manufacturers And Partners - Why Alfa Laval?
Global industry leader
Founded in 1883, Alfa Laval has led the way in centrifugal separation technology with continuous breakthroughs, and our high-performance decanter centrifuge is one of them. We have had practical experience with the design and manufacture of decanter centrifuges since the 50s. Today, with facilities all over the world, Alfa Laval is in a position to provide customers with superior products, superior service and superior results at any location.
Advanced material and technology
Alfa Laval uses high-grade stainless steel for all parts that come into contact with the solid-liquid separation process, in order to avoid any risk of the corrosion associated with the use of carbon steel.
Rotating components of Alfa Laval decanter centrifuges exposed to high stress are machined from high-strength centrifugally cast stainless steel. This ensures castings with a uniform grain structure free from flaws and defects as well as a completely weld-free finished component. The results are maximum strength, unparalleled reliability and a long service life.
All wear-prone areas of Alfa Laval centrifuges – the feed zone, solids discharge output zone, bowl and scroll – are protected by abrasion resistant material, selected to match the pattern of wear in each particular industrial process.
Continual refinement of the seal technology used in Alfa Laval decanter centrifuges is ensured by our technological resources. This is an area where Alfa Laval expertise and experience also make a key difference.
Service
As a decanter centrifuge manufacturer and solution provider, Alfa Laval has full control over the entire supply chain, which means that we can provide customers with response times, availability and lead times that are second to none.
Our worldwide service capabilities and vast experience with the contract maintenance and service of decanter centrifuges ensure that any service work required involves the absolute minimum of disturbance to operations.
For customized service solutions, our performance agreement can be tailored to your specific needs, with the aim to maximize your performance and reduce your operating costs.
Choose decanter according to your industry/application
Chemical decanters
Ethanol decanters
Food and beverage decanters
Oil & Gas decanters
Starch decanters
A well-run predictive maintenance plan will help you correct small service issues well before they turn into major problems. This can save you time, money, and the stress of an unplanned shutdown. Learn how to make the change in this on demand webinar.
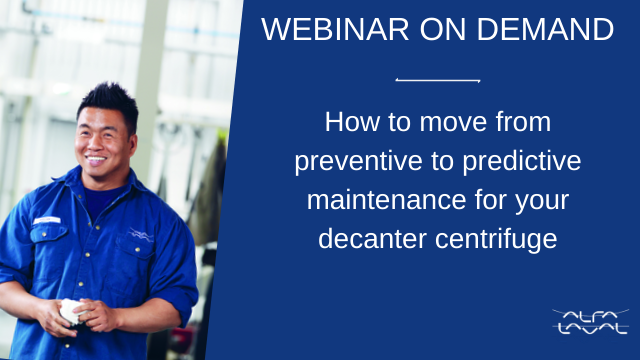
Maximize operating reliability with Alfa Laval IoT Services
Alfa Laval’s IoT Services is a range of digital services that maximizes operating reliability and uptime in food & beverage processing plants.
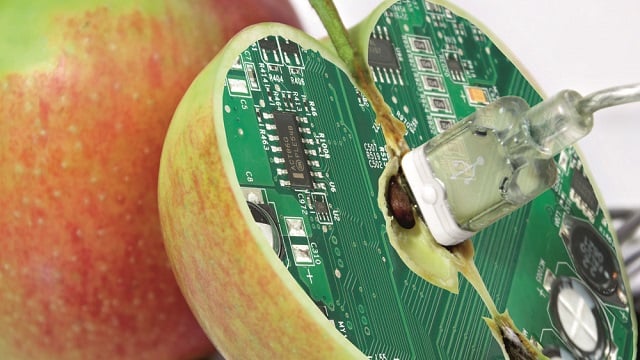
Minimize operating cost with Alfa Laval IoT Services
Alfa Laval’s IoT Services is a range of digital services aiming to reduce operating costs and maximize operating reliability in wastewater plants. Our Connectivity Solutions taking advantages of Industrial Internet of Things (IIoTs) technologies help us serve you better in domains such as predictive preventive maintenance, remote control, optimisation and more.
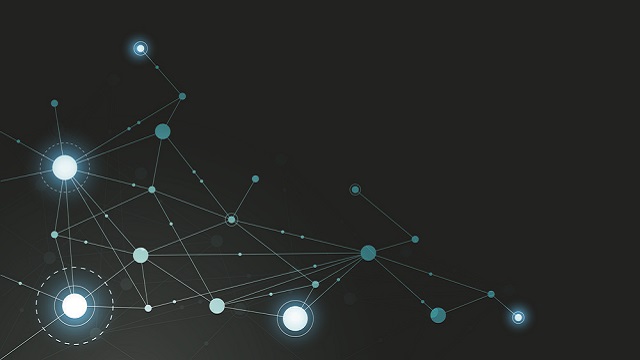