Improve efficiency and sustainability at minimal cost
Heating and cooling are essential functions in a refinery and have a profound effect on overall plant efficiency and profitability. Alfa Laval’s heat transfer solutions not only let you maximize the energy efficiency of your plant, they also improve your processes in terms of plant capacity, product yield and quality, cycle length, utility consumption, and environmental sustainability – all at minimal investment cost.
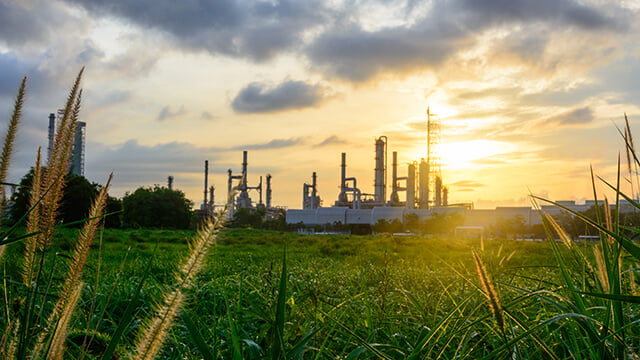
A new level of performance
Our compact, heat exchangers are key components in most of our solutions. They offer a unique combination of exceptional heat transfer efficiency, low pressure drop and high resistance to fouling.
A single Compabloc heat exchanger can replace up to eight shell-and-tubes connected in series. This means a heat transfer area equivalent to 4,000 m2 in a shell-and-tube solution can be installed in a plot space of just 3 m2, with a major impact on the performance of your processes.
More than just heat exchanger savings
The performance of our heat exchangers creates possibilities to completely rethink and optimize all types of refinery processes. Old rules of thumb no longer apply, and you can implement fundamental process design changes that have a radical effect on overall process efficiency, project ROI and environmental sustainability.
The greatest gains are won when entire processes are optimized, and not just individual heat exchanger services. By combining Alfa Laval’s process know-how and experience with the advantage of the heat exchanger capabilities, you create synergies with substantial positive effects.
Compact heat exchangers vs. shell-and-tubes
- 3-5 times higher heat transfer efficiency
- Down to 3°C (5.4°F) hot or cold approach temperature
- Up to eight shell-and-tube heat exchangers in series can be replaced by a single Alfa Laval heat exchanger
80-90% lower flooded weight - Much lower pressure drop in heat recovery and condensing services
- Up to three times longer operation between cleanings for high-fouling services
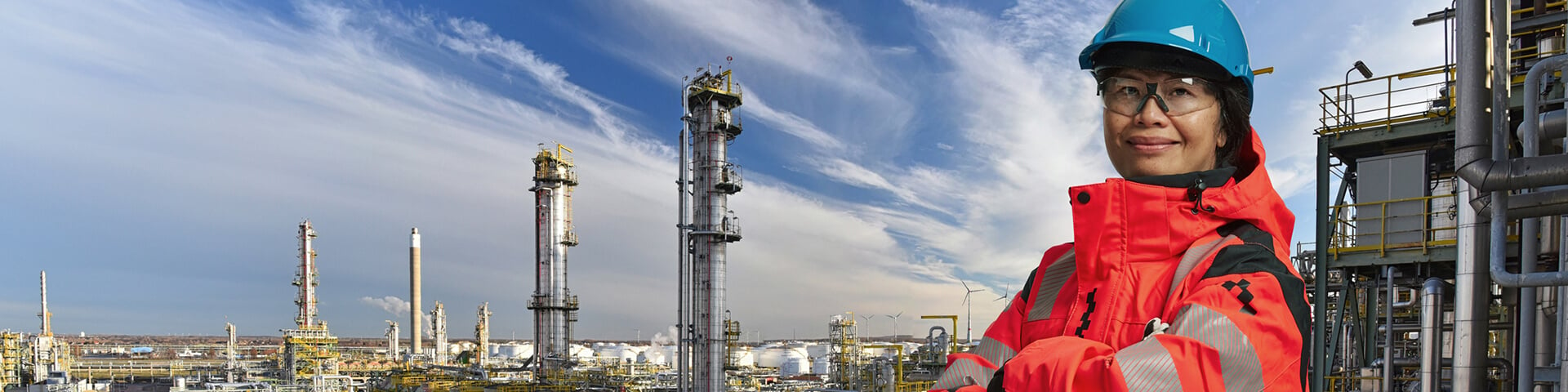
Increase capacity
Bottlenecks in equipment such as feed pumps, fired heaters or final coolers can often be resolved by maximizing feed preheating, using energy recovered from hot fractions, with minimal heat exchanger pressure drop.
Limitations in compressor or vacuum systems can often be overcome by increasing the vapour cooling/condensing capacity with more efficient heat exchangers.
Payback times for capacity improvement projects are normally less than 12 months, thanks to the high values generated.
Improve product yield and quality
More efficient separation in fractionation and stripping columns increases product yield and quality. With our condensing solutions, overhead vapours can be condensed at minimal saturation pressure and with the lowest pressure drop. This enables a pressure reduction in the flash zone of the column, resulting in a better split between products with similar boiling temperatures.
To further increase the yield of light products, the condenser can be designed with additional cooling capacity to minimize the amount of heavy hydrocarbons lost as off-gas.
Payback times for these types of investments are typically less than 12 months.
Boost energy efficiency
Up to 50% of a refinery’s operating cost is spent on energy. This can be reduced by up to 23% when implementing Alfa Laval solutions that maximize energy recovery and transformation of low-grade heat. An example of the latter is when energy in overhead vapour is used for producing steam or process water, preheating boiler feed water or district heating.
Greater energy recovery from hot fractions also reduces the load on cooling duties, generating savings in air cooler or trim cooler utility consumption.
Energy efficiency projects often result in improvements in capacity, product yield and quality as well, shortening payback times to less than 12 months.
Improve reliability and life cycle cost
When Alfa Laval implements solutions in your processes, you can rest assure that they are already technically proven and designed based on our vast experience of optimizing refineries all over the world.
We offer solutions where the technical risk is non-existent or is well-calculated and at an acceptable level. This prevents jeopardizing the reliability of your plant when improving the efficiency of your processes.
Based on Alfa Laval recommendations and our full commitment to support and follow up on the installation, operation and maintenance of our solutions, we also make sure that you get the highest availability and lowest life-cycle cost of your new investments.
Minimize CAPEX
Implementing Alfa Laval solutions while optimizing the process design also reduces the requirements on a wide range of expensive process equipment such as furnaces, reboilers, final coolers, chillers, steam boilers, cooling water systems, compressors, vacuum systems, and pumps, leading to major cost savings.
New investment using a modularized design will significantly reduce the costs for installation and transport, due to the minimal footprint and flooded weight.
Improve environmental sustainability
Higher energy efficiency in your processes reduces fuel and steam consumption in your plant, which in turn results in lower CO2 emissions. In addition to the positive effect on the environment, this can also improve your bottom line if your plant operates under an emissions trading system. It can further offer a solution for your permit to operate. If you are eligible for government funding for CO2 reduction projects, it might help you improve the ROI of your project.
Alfa Laval solutions are also used to maximize the performance of sulphur recovery and carbon capture units. In addition, our process optimizations will minimize heavy hydrocarbons in off-gas and reduce cooling water consumption.
20% higher capacity
A Canadian refinery installed an Alfa Laval Compabloc as combined feed effluent heat exchanger in its 22 kbbl/day cracked naphtha hydrotreatment unit. This increased the preheating of the reactor feed and reduced the load on the feed pump, resulting in more than 20% higher capacity. The investment paid off in less than 12 months.
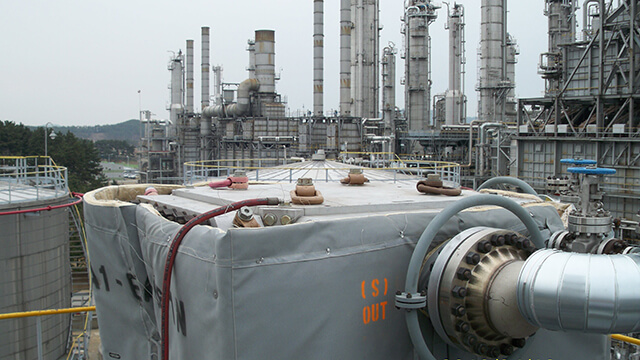
2,200,000 USD in annual energy savings
Swedish refining company Preem replaced four shell-and-tubes in the 220 kbbl/day CDU preheating train in its refinery in Lysekil with one Alfa Laval Compabloc. This increased energy recovery from 15.6 to 22.6 MW, reduced fuel cost by 2.2 MUSD/year and cut CO2 emissions by 14,600 tonnes/year.
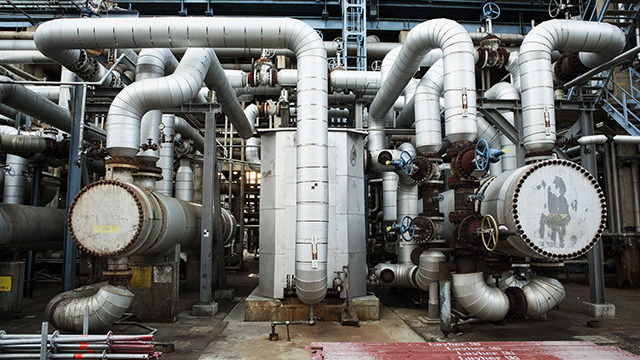
1,150,000 USD in project savings
A US refinery designed the refrigeration loop of a new 12 kbbl/day alkylation unit around an Alfa Laval Compabloc. This made it possible to reduce the condensation pressure by more than 1 bar, compared to a shell-and-tube solution, which in turn reduced the cost of the compressor by 1,500,000 USD. Even if the cost for the heat exchanger became higher with this design, the net saving was 1,150,000 USD.
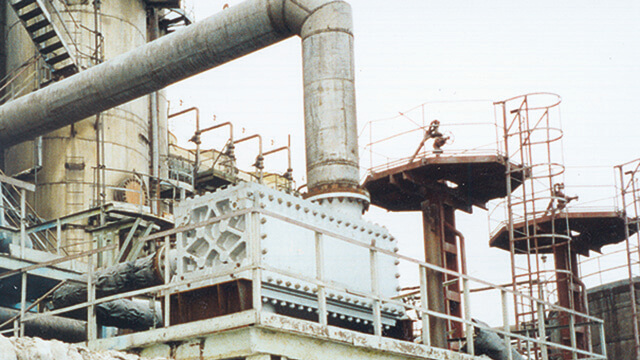
Improved product yield and quality
A European refinery replaced four shell-and-tube OVHD condensers in a 120 kbbl/day CDU with two Alfa Laval Compablocs with lower pressure drop. This made it possible to reduce the pressure in the flash zone by 0.3 bar, reducing the temperature of the 95% naphtha by 10°C (18°F) and increasing the naphtha/kerosene split by 5°C (9°F).
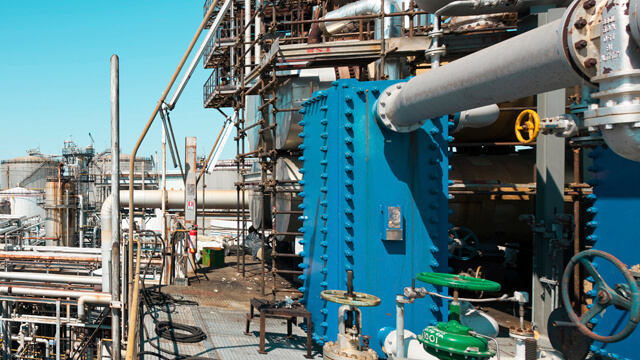