P3
Alfa Laval’s P3 range of decanter centrifuges is built for the toughest applications and is specifically developed for solid-liquid separation in the mining and mineral industry. Every detail has been designed to deal with the harsh conditions found in mining, mineral processing and tailings treatment applications.
Alfa Laval’s P3 decanter is well suited for a wide range of mining and mineral applications such as:
- Tailings treatment
- Recovery of water, chemicals or minerals
- Treatment of slurries with finer particles
- Where dry stacking with stackable solids is required
- Installations where flexibility and movability are required
- Where environmental concerns are important
Alfa Laval P3 heavy-duty decanter centrifuges are built with carefully selected components such as Duplex stainless steel, heavy-duty bearings and a stiff box beam frame. All interior parts of a P3 decanter centrifuge exposed to abrasion are protected by replaceable tungsten carbide tiles to eliminate problems. The feed and outlet zones have been designed for smooth acceleration of the solids to minimize wear and secure an efficient separation process.
The P3 model offers the highest throughput on the market and handles extremely high solids loads. The special deep-pond design in combination with the unique conveyor and the optimized cone angle configuration allows the P3 to handle volumes far beyond the capacity of any other decanter centrifuge. With the P3 decanter you get:
- High cake dryness, producing a stackable cake
- Very high capacity and small installation area
- Fully wear protected throughout the separation process inside the decanter
- Robust design and high reliability
- Lowest power consumption for any mining and mineral decanter
How it works
Alfa Laval P3 decanter centrifuges are specifically designed to separate mining and mineral slurries, tailings and sludge into a solid phase and liquid phases.
Separation takes place in a horizontal cylindrical bowl equipped with a scroll conveyor. The product is led into the bowl through a stationary inlet tube and is then smoothly accelerated in a full-flow feed zone design. Centrifugal forces of up to 3,500 G make the solids accumulate on the inner surface of the bowl.
The conveyor rotates in the same direction as the bowl, but at a different speed. This moves the solids towards the conical end of the bowl. The solids leave the bowl through the solids discharge openings into the casing.
Separation takes place throughout the length of the cylindrical part of the bowl, and the clarified liquid leaves the bowl by flowing over adjustable plate dams into the casing.
A well-run predictive maintenance plan will help you correct small service issues well before they turn into major problems. This can save you time, money, and the stress of an unplanned shutdown. Learn how to make the change in this on demand webinar.
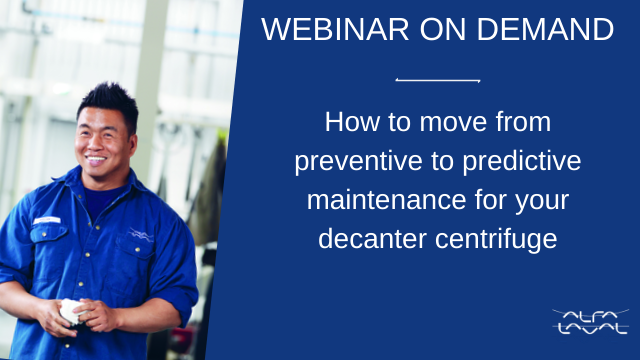