Unique features
Advanced engineering for the most energy-efficient heat transfer solutions
Alfa Laval's gasketed plate-and-frame heat exchangers stand out in the realm of heat transfer solutions due to an array of unique features that redefine efficiency and versatility. Our heat exchangers incorporate cutting-edge technologies, including specialized gasket designs and precision-engineered plates, to ensure optimal thermal performance across diverse applications. Our commitment to innovation is evident in features such as turbulence-promoting patterns on the plates, fostering efficient heat exchange while minimizing fouling. The modular frame design allows for adaptability to varying process requirements and simplifies maintenance tasks. Additionally, the incorporation of advanced sealing technologies ensures a secure and leak-free operation.
Browse videos on common types of gasketed plate-and-frame heat exchangers and their unique features below. Or contact our team for a more in-depth discussion on your needs.
Common types of GPHEs
Explore Alfa Laval’s collection of informative videos showcasing the capabilities of our conventional gasketed plate heat exchangers and plate-and-frame heat exchangers used in other applications.
Conventional gasketed plate heat exchangers
Alfa Laval offers a wide range of conventional heat exchangers, including gasketed plate-and-frame heat exchangers. Designed to efficiently transfer heat between fluids, making them versatile solutions for various industrial applications, our conventional line of gasketed plate heat exchangers are available in 1-pass, 2-pass or steam heater configuration.
Hygienic applications
Alfa Laval hygienic gasketed plate-and-frame heat exchangers are designed to meet the highest hygiene standards. Our hygienic line is available in a 1-flow or multi-section pasteurizer configuration to maximize heat recovery in hygienic applications.
Specific applications
Alfa Laval’s AlfaCond is a gasketed plate-and-frame heat exchanger designed to efficiently condense steam or other vapors into liquid form. By effectively converting steam into liquid, it facilitates the reuse of valuable energy, reducing both operational costs and environmental impact. It is widely used in a multitude of applications, including power plants, petrochemical refineries, food processing facilities and many more. Its versatility and reliability make it a go-to choice for industries that require efficient heat recovery and sustainable energy solutions.
How GPHEs work
Liquid/Liquid GPHE
Working principle
The Alfa Laval liquid/liquid 1-pass gasketed plate-and-frame heat exchanger operates on a counter-current flow principle, where hot fluid enters from the top and exits from the bottom, while cold fluid enters from the bottom and exits from the top. The heat transfer plates have specially designed sealing gaskets that guide the fluids to flow counter-currently in alternating channels. The distribution area, such as the patented CurveFlowTM, ensures even fluid flow over the plates, enhancing heat transfer efficiency and minimizing maldistribution and fouling.
Benefits
This configuration maximizes heat recovery and allows for a close temperature approach, making plate-and-frame heat exchangers more thermally efficient compared to tubular heat exchangers because of their allowance for temperature cross, where the hot outlet can reach a lower temperature than the cold outlet. For very heat sensitive media, co-current flow is used, so that the coldest fluid meets the hottest fluid when entering the heat exchanger, minimizing the risk of overheating or freezing sensitive media.
Steam heater GPHE
Working principle
An Alfa Laval gasketed plate-and-frame heat exchanger, when used as a steam heater, operates by allowing steam or vapor to enter from the upper connection and condensate to exit from a connection beneath. Simultaneously, cold liquid enters from one of the lower connections and exits from the connection above. Heat is transferred from the condensing steam/vapor to the cold liquid as they flow counter-currently through specially designed heat transfer plates with sealing gaskets.
Benefits
Our CurveFlowTM distribution area ensures an even flow of fluids over the plates, maximizing heat transfer efficiency while minimizing maldistribution and fouling. This design facilitates the rapid filling of the entire cross-section of the plates by the fluids.
2-Pass GPHE
Working principle
The Alfa Laval liquid/liquid 2-pass gasketed plate-and-frame heat exchanger operates on a counter-current flow principle, with a turning plate directing the fluid into two passes. Hot liquid enters through the frame plate, runs through the heat exchanger in two passes, and exits through the pressure plate. Simultaneously, cold liquid enters through the pressure plate and exits through the frame plate. Heat is transferred from the hot to the cold media, and temperature cross allows the hot outlet to reach a lower temperature than the cold outlet, making it more thermally efficient than tubular heat exchangers.
Benefits
Counter-current flow enables maximum heat recovery possibilities and very close temperature approach can be achieved. With this design, the coldest fluid meets the hottest fluid when entering the heat exchanger, minimizing the risk of overheating or freezing sensitive media.
Features that matter
There's a common misconception in the industry that all gasketed plate-and-frame heat exchangers are the same, no matter the brand. However, there are quite a few design features that can have a significant impact on your operation. The plate-and-frame features highlighted below are important components to look for in a heat exchanger and, when combined, offer extensive benefits, including:
- Reduced installation, maintenance and spare parts costs
- Reduced energy costs
- Decreased downtime
- Higher production output
- Increased staff safety
Plate features
Alfa Laval’s plates feature intricate patterns that enhance heat transfer, optimizing the exchange process and are available with various pressing depths, angles of chevron pattern and various corrugation shapes, all carefully designed and selected to achieve optimal performance. Depending on the application, each product range has its own specific plate features. To learn more about Alfa Laval plate technology and design, read more below. [Anchor link to content at bottom of page]
CurveFlow™
The CurveFlow™ distribution area optimizes the flow of media for better utilization of the whole plate surface. Improving the flow with more even distribution eliminates dead spots, providing higher thermal efficiency with reduced risk of fouling. This in turn means energy savings, lower maintenance costs and less time worrying about unplanned stops.
ClipGrip™
ClipGrip™ gaskets offers superior fastening to the plate. Not only do the next-generation gaskets stay in place better than before, but they are also easier to mount in the first place. The unique design prevents snaking of plates at closing and the tangling of new gasket sets. Maintenance of the heat exchanger goes faster, plates and gaskets last longer, and you save money as a result.
Five-point alignment
Alfa Laval’s unique five-point alignment system ensures perfect plate alignment when closing the unit, while simultaneously making it quick and easy to remove plates during maintenance. Excellent plate positioning secures reliable mechanical performance and helps extend the life of your equipment.
Offset gasket groove
The next generation of gasketed plate heat exchangers is designed with a gasket groove in a special zig-zag pattern that offers the greatest possible heat transfer area. Better utilization of the whole plate reduces the number of plates required for optimal performance and ensures maximum thermal efficiency for still greater energy savings.
OmegaPort™
The OmegaPort™ noncircular inlet and outlet offers two ways to save on energy: both higher thermal efficiency and reduced pump costs. That’s because it enhances the flow of media to give increased throughput, lower pressure drop and optimal utilization of the plate surface.
RefTight™
The RefTight™ sealing system enables enhanced, long-term performance in applications with high pressures and temperatures. The weld is positioned outside the separate ring gasket groove, ensuring reliable sealing as well as extended gasket lifetime and prolonged service intervals.
FlexFlow™
The FlexFlow™ plate design improves thermal efficiency and optimizes pressure drop utilization. The asymmetric channels eliminate the compromise between thermal efficiency and pressure drop for duties with different hydraulic loads on the two sides of the heat exchanger. The result is up to 30% higher efficiency along with reduced fouling, for long-term, cost-effective performance.
PowerArc™
The PowerArc™ plate pattern divider is a feature in the bigger plates of Alfa Laval’s next-generation heat exchangers. This design ensures a more rigid plate, preventing plate elongation and securing perfect alignment. As a result, the risk for leaks or damage to the plate is significantly reduced, meaning you can expect longer operation from every plate in the pack. Additionally, the increased rigidity makes handling plates during maintenance a safer and easier process.
SteerLock™
The SteerLock™ plate alignment ensures reliable plate positioning and easy service. It also secures the plate pack when exposed to pressure and temperature during operation. If the unit is disassembled for maintenance, the smart design simplifies the picking of plates when they are about to be hung back.
Frame features
Alfa Laval’s frames are meticulously designed to provide structural integrity, ease of maintenance and optimal thermal performance and boast a modular construction, allowing for flexibility in adapting to various process requirements and facilitating easy expansion. Furthermore, our plate heat exchangers incorporate advanced sealing technologies within the frame, ensuring a secure and leak-free operation.
T-bar roller
In the next-generation plate heat exchanger, Alfa Laval has replaced the traditional roller function built on top of the carrying bar with a T-bar roller. The pressure plate roller is mounted under the carrying bar, decreasing the height of the heat exchanger and making maintenance simpler and more cost-effective. This design also protects the roller from falling dust and debris, which prevents jamming, minimizes the potential for damage to the frame and ensures easy opening and closing of the unit when required.
Compact frame
The Compact frame feature offers more capacity in a smaller footprint. The smart guiding bar enables a maximum number of plates or cassettes in the frame while keeping the service area requirements down to a minimum. The design enables a faster and safer service which minimizes downtime and reduces maintenance costs.
Bearing boxes
Alfa Laval’s large and medium model gasketed plate heat exchangers employ tightening bolts with bearing boxes to reduce friction when opening and retightening the unit. This makes it possible for one person to easily and safely service the heat exchanger without the need for special tools. The bearing box thus offers significant advantages over competing solutions designed with a simple nut and washer, where maintenance is laborious, time-consuming and potentially hazardous.
Plate and gasket technology
The design of the corrugated plates optimizes heat transfer by providing a large but compact total surface area through which the heat can be drawn from one liquid or gas to another.
The heat transfer area of the plates is pressed in a corrugated herringbone pattern. When two plates are superimposed with opposing herringbone patterns, the helix-like flow and high turbulence results in high transfer coefficients and effective self-cleaning.
A change in the corrugation pattern enables the heat exchanger to be used in different processes, even those with very dirty media.
Distribution area
The plate distribution area ensures an even flow of fluid over the entire plate to maximize the heat transfer capability. An optimized flow distribution also reduces fouling and uneven temperature zones keeping the performance levels high over time without unnecessary energy losses, maintenance costs or unplanned stops.
Gaskets are key components in heat exchanger performance. We design the gasket and plate as one to assure an optimized seal. Each is tailored to the duty of the heat exchanger. The correct profile, width, thickness, and polymer type and compound make a world of difference in avoiding the risk of premature leakage or gasket or plate damage. Your benefits are prolonged gasket life, less downtime and lower maintenance costs.
Gasket profile
Gasket glue
Special plate types
Double-wall gasketed plate heat exchangers
Designed for use with fluids that cannot be allowed to mix. Prevents leaking fluid coming into contact with the fluid in the other circuit.
Wide-gap plates
Ideal for fluids containing fibers or coarse particles. Designed to eliminate bridging of solids in the entrance area.
Semi-welded plates
Enable aggressive and difficult fluids to be handled, and also extend the pressure range.
Diabon™ graphite non-metallic plates
A composite of fused graphite and fluoroplastic provides excellent resistance to corrosive materials.
Discover more watching our expert videos
Where would we be today without people who dare to challenge old ideas – the people willing to think outside the box? Setting new standards demands visionaries with know-how and a dedication to teamwork.
The advanced, new features of our heat exchangers are the work of talented experts at Alfa Laval. Let us introduce you to some of the team behind the next generation of gasketed plate heat exchangers.
Products applying the features
Carina introduces the next generation
Magnus introduces FlexFlow™
Mattias introduces SteerLock™
Kristina introduces Compact frame
Martin introduces CurveFlow™
Johan introduces ClipGrip™
Torgny introduces five-point alignment
Magnus introduces OmegaPort™
Jenny introduces the offset gasket groove
Sven introduces the T-bar roller
Göran introduces the bearing box
RefTight™ sealing system explained
Contact an expert
To learn more about your options or to get advice from our experts about which gasketed plate heat exchanger is the best fit for your business, contact us now.
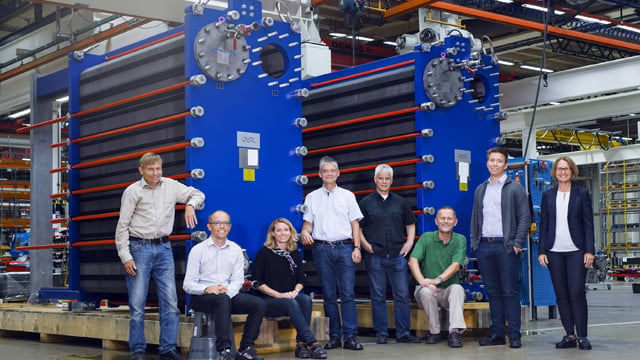