The 4 most common cleaning methods for cutting fluids
An article related to cutting fluids management.
DATE 2023-11-28Most machining and metalworking processes benefit from the use of a cutting fluid for cooling and lubrication, which maximizes the life of the cutting tool and prevents corrosion on machine parts. Today’s cutting fluids are designed for specific applications and often come in the form of oil-water emulsions.
But over time, water based cutting fluids become contaminated by unwanted oil, which can result in the growth of bacteria and fungi that damage tools, decrease precision and cause health hazards. In addition, microparticles from the machining or metalworking process can end up in the cutting fluid, resulting in a sand-blasting effect on the surfaces of components and tools.
To avoid these problems, cutting fluids should be cleaned and replaced regularly. To help you determine the best option for cleaning your cutting fluids, we’ve compiled a list of the four most common cutting fluid cleaning methods.
Centrifugation
High-speed centrifugal separators use centrifugal force to separate oil and solid contaminants from cutting fluids. Particles present in the cutting fluid are pressed against the walls of the separator by centrifugal force. The particles are then discharged manually or automatically from the bowl. The centrifugal force will also cause unwanted oil to separate from the cutting fluid. Cleaned cutting fluid is sent back into the machining or metalworking process while the unwanted oil is continuously discharged.
What to consider:
- High-speed centrifugal separators remove both unwanted oil and solids
- The initial investment is higher, but the operational cost is very low, which results in a low total cost of ownership (TCO)
- High-speed centrifugal separators handle even tiny particle sizes – much smaller than the best filters can manage
- There is no need for disposables such as filter cartridges
- Low maintenance gives more process uptime
- High-speed centrifugal separators only remove loosely emulsified oils – the cutting fluid emulsion is left intact
- Centrifugation can handle large cleaning volumes and withstand a temporary high influx of oil
Filtration
Cutting fluid filters often use paper bands of various mesh sizes as a cleaning method to capture solid particles. Particles larger than the mesh are captured and removed from the fluid, while the smaller ones remain. When the paper band is used up, it has to be removed, safely disposed of, and replaced.
What to consider:
- Filters don’t require much capital investment
- The need for disposables leads to higher operating costs
- Filters don’t remove oil, which means they need to be combined with coalescers or separators – otherwise you get a rapid growth of bacteria and fungi
- You need to comply with increasingly strict environmental regulations
- Filters only capture solids larger than the mesh size (typically 10–30 µm)
- Captured particles may be released again if the filter is exposed to pressure shocks at start-up or stop
- Filters need regular monitoring and changing to avoid clogging, which leads to downtime
- There can be fluctuations or reductions in pressure when filters are contaminated, which lead to decreased performance
Skimming
Oil skimmers are designed to remove oil floating on the cutting fluid’s surface. There are many different types of skimmers, but the basic cleaning principle is that floating oil adheres to a skimming medium such as a mop, rope, disk, tube or belt. The medium is then passed through a machine that wipes it clean and collects the oil.
What to consider:
- Oil skimmers are simple and low-cost solutions for removing small amounts of oil under stable conditions
- Solid contaminants are not removed
- Oil skimmers don’t handle changes in oil properties or throughput volumes very well
- A mixture of oil and water is removed – not just the oil
- Oil skimmers can’t handle medium to high amounts of free oil in the fluid
- Performance varies significantly depending on the oil used
- Oil skimmers can’t be used if certain additives or surfactants are present
Coalescence
Coalescers are used to perform coalescence, which is the process of causing liquid emulsified small droplets to form larger droplets. The larger droplets are then drained away gravitationally.
What to consider:
- Coalescers are easy to install and maintain
- The capital investment is low
- The effectiveness is limited, which can lead to process inefficiency and higher lifetime costs
- Solid contaminants are not removed
- Cutting fluids have to be very clean from particles to enable coalescence
- Coalescers can’t be used if certain additives or surfactants are present
- Coalescers can’t cope with high amounts of free oil in the fluid
In combination with the four cutting fluid cleaning methods described above, a filter that removes the largest particles should always be used – even if you use another filter to remove smaller particles.
Whatever metalworking application you have, Alfa Laval has a centrifugal separation system that can keep your cutting fluids clean from oil. and we’ll set you up with an expert who can help you choose the right solution for your needs.
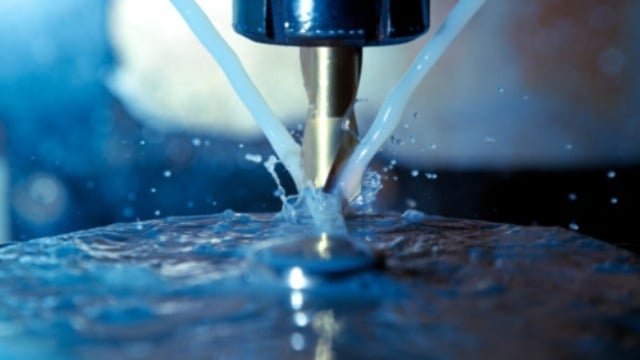