MF spiral
Alfa Laval microfiltration spiral membranes (MF) are proven solutions for efficient removal of dispersed solids. The unique construction of polypropylene support material in a sanitary, full-fit design ensures optimum filtration. There are different types of microfiltration membranes and various combinations of length, diameter and feed spacer size to ensure the right performance for your application.
Efficient filtration without affecting the balance of the components dissolved in the stream
- Cost effective operation thanks to low energy consumption
- Efficient – no need to replace/dispose of the cartridges or consumables used in traditional dead-end filtration
- Extremely durable – excellent chemical and thermal stability and service life up to several years
- Flexible – for a broad spectrum of membrane materials and pore sizes
- Minimal floor space required - compact design
A wide range of microfiltration membranes
The microfiltration membranes are available in two different materials and a number of pore sizes to ensure that you find the right one for your application.
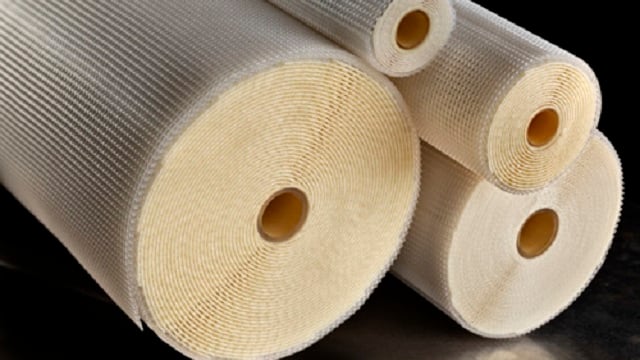
MFG series
The MFG microfiltration membrane is made of polysulphone polymer. The MFG1 pore size is 0.1 µm while the MFG2 is 0.2 µm.
MFP series
The MFP microfiltration membrane is made of fluoro polymer. MFP2 has a pore size of 0.2 µm and MFP5 of 0.5 µm.
We can offer products with Halal certificates upon request.
Our spiral wound membrane materials are compliant with all major regulations
All membrane materials used for both flat sheet and spiral wound configurations comply with EU Regulation (EC) 1935/2004, EU Regulation 10/2011, EU Regulation (EC) 2023/2006 and FDA regulations (CFR) Title 21, and are suitable for use in food and pharmaceutical processing applications. Compliance also extends to the related equipment and fittings, including items such as plate-and-frame units, element housings and pumps.
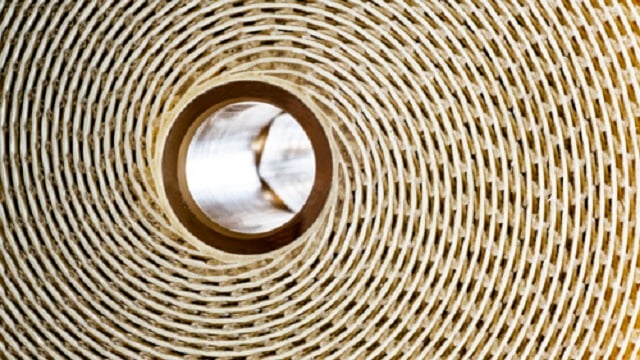
How it works
Spiral membrane technology
The basic technology behind membrane filtration involves using a semi-permeable membrane to separate a liquid into two distinct streams.
Pumping this liquid across the surface of the membrane creates a positive trans-membrane pressure that allows any components smaller than the porosity of the membrane to pass through, forming the permeate.
Any components larger than the pore size simply cannot pass through, and remain behind in what is called the retentate. The surface of the membrane is kept free of blockages by the force of the liquid flow moving parallel to the membrane surface.
Construction of the spiral membrane
A spiral membrane comprises of a number of membrane 'envelopes' with 2 membrane sheets separated by a permeate spacer mesh, each glued to a central permeate collection tube.
Between each pair of envelopes there is a spacer which creates the feed channel, allowing the feed to flow across the length of the spiral wound membrane, whilst the permeate passing through the membrane into the membrane envelope flows in a spiral pattern to the permeate collection tube.
Red = Feed/retentate
Yellow = Permeate
Shown above is the flow pattern in a spiral membrane, where red represents the feed/retentate and yellow the permeate.