Condition monitoring prevented the product loss of 288,000 bottles at Britvic facility
Ensuring high uptime is a first priority at Britvic’s production plants. At their plant in Rugby, Great Britain, Britvic successfully prevented pump failure, optimized asset performance and ensured continuous production by using Alfa Laval Analytics for online condition monitoring. Chris Heslop, Engineering Specialist at the Rugby facility, remarked: "Just this one notification paid for our entire investment in the condition monitoring solution and the first year of our Analytics subscription.” The user-friendly and cost-effective Analytics for online condition monitoring brought peace of mind and enabled Britvic to maintain pumps at their peak performance during 24/7 production.
DATE 2024-10-31Timely inspection and repair of utmost importance
At the Britvic facility in Rugby, Great Britain, hundreds of pumps ensure the daily production of a diverse range of soft drinks. Vast and complex production lines operate around the clock, and even a single pump malfunction can bring production to a halt for several hours.
The Britvic production team looked for a condition monitoring system that would enable them to focus on specific, critical parts of production, leaving time for other important tasks. Timely inspection and repair are especially important at the Rugby facility, given that the plant operates a wide variety of pump types and cannot keep spare parts for all of them. Early warning of potential failure is therefore extremely important to plan and facilitate prompt maintenance to avoid downtime.
Preventing sudden pump failure
To prevent potential pump failure, the Britvic team decided to install the Alfa Laval condition monitoring solution on 107 centrifugal pumps when the opportunity arose. In just a few months, the system proved its worth when a notification came through, warning of a potential issue with a pump that would never have been discovered without the monitoring system. The notification enabled the technical team to inspect and repair the pump before an actual failure occurred.
Just this one notification paid for our entire investment in the condition monitoring solution and the first year of our Analytics subscription”, said Chris Heslop, Engineering Specialist at the Rugby facility.
Britvic purchased the condition monitoring hardware and installed the CM sensors on 107 LKH pumps.
Saved six hours of unplanned downtime
Thanks to the Analytics notification, the technical team could take out the critical pump for maintenance. It took just 45 minutes to disassemble, repair, and reinstall the pump, which saved six hours of unplanned downtime and prevented a production loss of 288,000 bottles of soft drink.
Supporting Britvic’s sustainability strategy
One of Britvic's sustainability targets is to reduce the water consumption ratio in manufacturing year after year, and water efficiency projects are carried out across sites to achieve this.
The implementation of condition monitoring helped improve the water efficiency at the Rugby facility. Thetimely detection and repair of the pump saved four hours of unexpected CIP (Cleaning-In-Place) and, consequently, 2,000 litres of water plus energy and chemicals used in the CIP process.
The early fault detection also improved the pump life cycle.
Considering expanding condition monitoring
With the positive experiences gained from using Analytics for online condition monitoring, the Rugby facility is contemplating expanding the solution to include more pumps within the manufacturing area. Day by day, the collection of data and helpful insights continues to grow, enabling the early detection of potential machine failures and the identification of root causes.
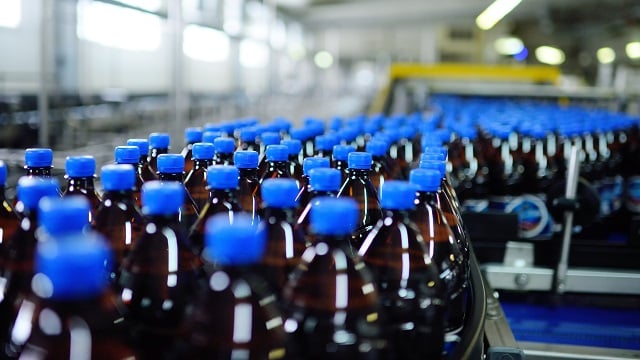
Innovation highlight
Facts about Britvic
Britvic is an international beverage business founded in England in the 1930s and grown into a global organization with 38 brands sold in over 100 countries. Britvic operates factories in Great Britain, Brazil, France and Ireland. In Great Britain and Ireland Britvic holds an exclusive licence with PepsiCo to produce and sell Pepsi MAX, 7UP, Rockstar Energy and Lipton Ice-Tea.
Facts about Alfa Laval Analytics for online condition monitoring solution
Britvic purchased the condition monitoring hardware and installed the CM sensors on 107 LKH pumps. The CM sensors measure pump vibrations and send data to the CM Connect gateway, which can collect data from up to ten CM sensors. CM Connect then sends data to the AI-based Alfa Laval Analytics for online condition monitoring. The pump data is presented in a real-time dashboard, and operators receive notifications in case of irregularities.
The installation of the entire condition monitoring solution at the Britvic facility was completed in less than two weeks, providing the Britvic team with instant access to data.
Why condition monitoring system?
A single notification paid back the entire condition monitoring solution
At the Britvic factory, Analytics for online condition monitoring notified the operators of an issue with a pump that would likely have gone unnoticed, if the condition monitoring system had not been running. Timely inspection and repair of a pump impeller resulted in substantial savings:
Saved production loss of 288,000 bottles
6 hours saved of unplanned downtime
2,000 repair time litres of water saved
4 hours saved of extra CIP
Saved extended 2,000 repair time